Bioreactor Controller Rebuild
ILS helped a leading manufacturer of USDA-licensed biologicals un-retire an 800L reactor
Project Brief
Our client is a leading contract manufacturer of USDA-licensed biologicals for both large and small animals. Much of their work is in the production of cattle vaccines and drugs for companion animals. Like most corporations today, this company’s policy prevents the use of their corporate identity in the marketing of other companies, and so must remain anonymous.
The manufacturer had an 800 liter microbial, 30+ year-old stainless steel, steam-in-place (SIP) vessel that was mechanically sound but in desperate need of a new bioreactor controller. The old controller had become unreliable, causing the vessel to sit unused for over a year. Being a contract manufacturer, they needed to replace the production capability and required flexible controls for the varying products their customers produced. Of foremost concern was the cost to replace the idle system.
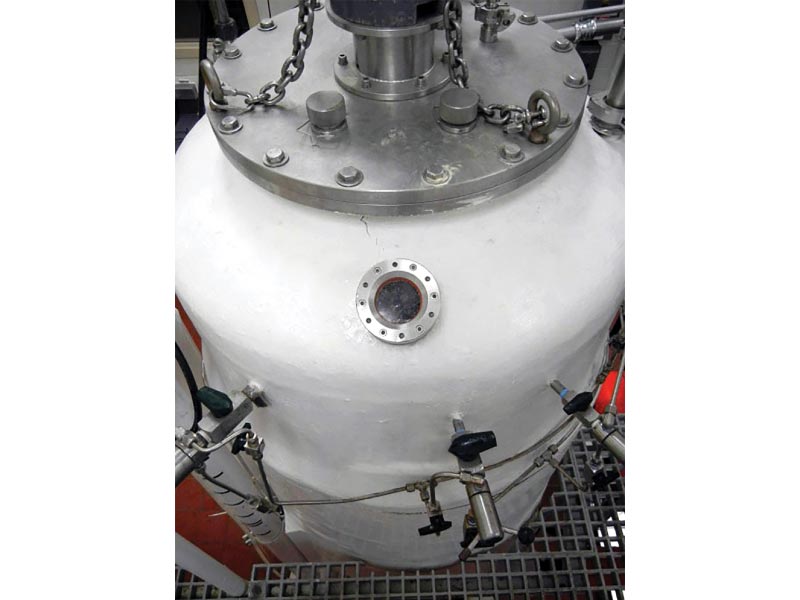
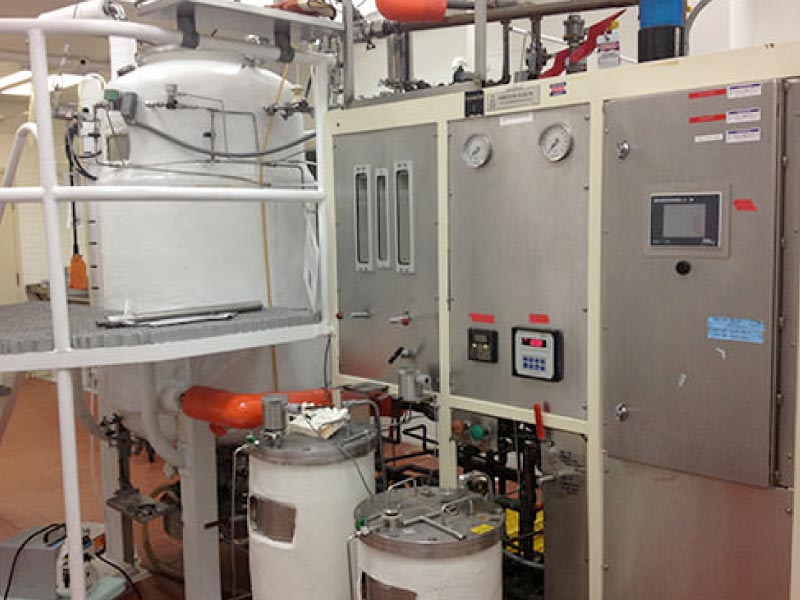
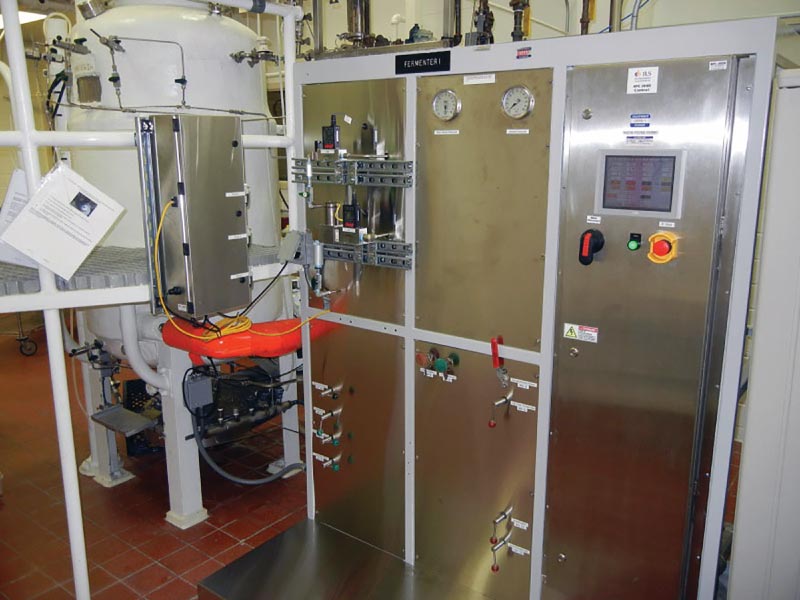
Click and drag the center line to see before and after photos
Hardware: Bioreactor Controller Rebuild
A new vessel and controller package was quoted at well over $1.2 million dollars. Rather than start over, the manufacturer opted to have ILS Automation provide a new controller for a fraction of the cost.
ILS worked closely with the client and their department supervisor to define the operating specifications for the new controller. The solution was for the older control system to be removed and replaced with an AFC 2000, ILS’s semi-custom replacement bioreactor controller. As a way to help keep the project costs down, ILS customized their controller design to fit seamlessly into the existing stainless cabinetry.
Software: Batch Expert+ SCADA
Integral to the controller design is the implementation of Batch Expert+ (BE+) from ILS Automation. BE+ is a state-of-the-art, web-based Supervisory Control and Data Acquisition (SCADA) system designed specifically for the fermentation and cell culture industries. The software provides supervisory control of the reactor, recipe management, a true SQL historian, and provides trending, alarming, and batch reporting, all customizable.
Batch Expert+ is built on top of Ignition, a uniquely scalable SCADA platform from Inductive Automation. Ignition allows BE+ to scale to accommodate an entire facility, including multiple brands of reactors, mass spectrometers, assay and other external data, while monitoring separation units, chillers, freezers, and other devices.
As a contract manufacturing facility, it is critical that the manufacturer is able to provide full documentation and data logs for their customers’ production runs. With BE+, any deviations in the run are automatically documented. These detailed records give the manufacturer’s customers added confidence in each batch, allowing them to accept runs with minor deviations they might otherwise reject.
Access to BE+ can be both local and remote, allowing users to check and modify batches from their office, at home, or even from their mobile device.
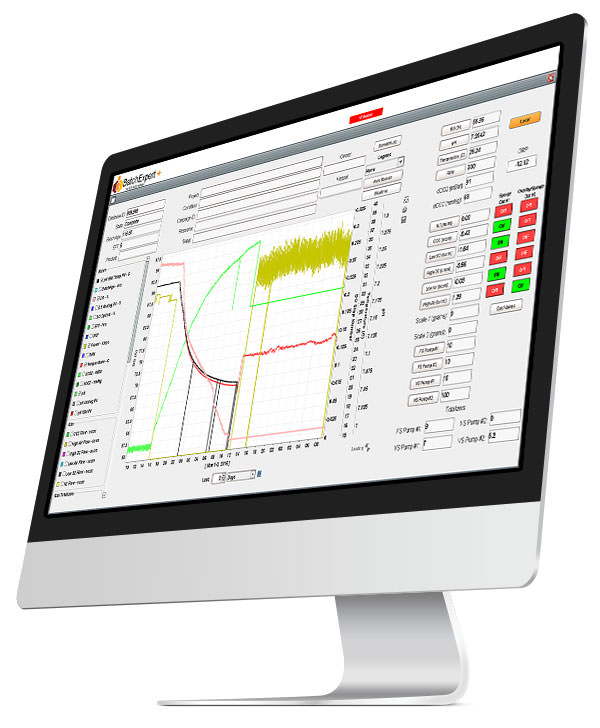
250L System
No sooner than the 30L system was completed and our Batch Expert+ software was installed, the next two retired systems were purchased. No sooner than the 30L system was completed and our Batch Expert+ software was installed, the next two retired systems were purchased.
No sooner than the 30L system was completed and our Batch Expert+ software was installed, the next two retired systems were purchased.
No sooner than the 30L system was completed and our Batch Expert+ software was installed, the next two retired systems were purchased.
No sooner than the 30L system was completed and our Batch Expert+ software was installed, the next two retired systems were purchased.
No sooner than the 30L system was completed and our Batch Expert+ software was installed, the next two retired systems were purchased.
No sooner than the 30L system was completed and our Batch Expert+ software was installed, the next two retired systems were purchased.
No sooner than the 30L system was completed and our Batch Expert+ software was installed, the next two retired systems were purchased.
No sooner than the 30L system was completed and our Batch Expert+ software was installed, the next two retired systems were purchased.
1500L System
No sooner than the 30L system was completed and our Batch Expert+ software was installed, the next two retired systems were purchased. No sooner than the 30L system was completed and our Batch Expert+ software was installed, the next two retired systems were purchased.
No sooner than the 30L system was completed and our Batch Expert+ software was installed, the next two retired systems were purchased.
No sooner than the 30L system was completed and our Batch Expert+ software was installed, the next two retired systems were purchased.
No sooner than the 30L system was completed and our Batch Expert+ software was installed, the next two retired systems were purchased.
No sooner than the 30L system was completed and our Batch Expert+ software was installed, the next two retired systems were purchased.
No sooner than the 30L system was completed and our Batch Expert+ software was installed, the next two retired systems were purchased.
No sooner than the 30L system was completed and our Batch Expert+ software was installed, the next two retired systems were purchased.
No sooner than the 30L system was completed and our Batch Expert+ software was installed, the next two retired systems were purchased.
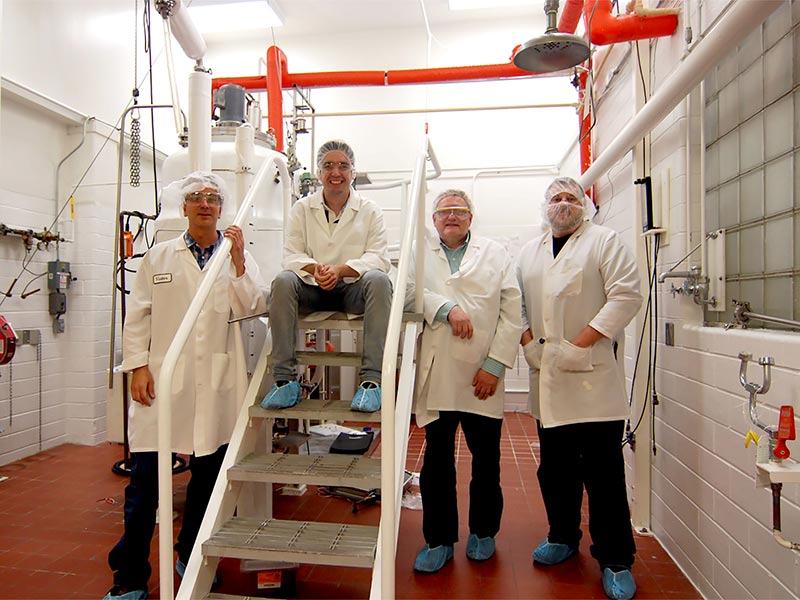
ILS team members on site
A Custom Engineering Solution
An existing or used system with a retrofit bioreactor controller typically saves 50-90% vs the cost of a new system.

Savings
Saved approximately $1.5 million by retrofitting used equipment vs buying new.

Yield Increase
After the rebuild, a previously dormant 800L bioreactor is able to be used again, allowing this client to ramp up production.

Remote Access
Users can now manage controllers remotely when they’re out of the office.